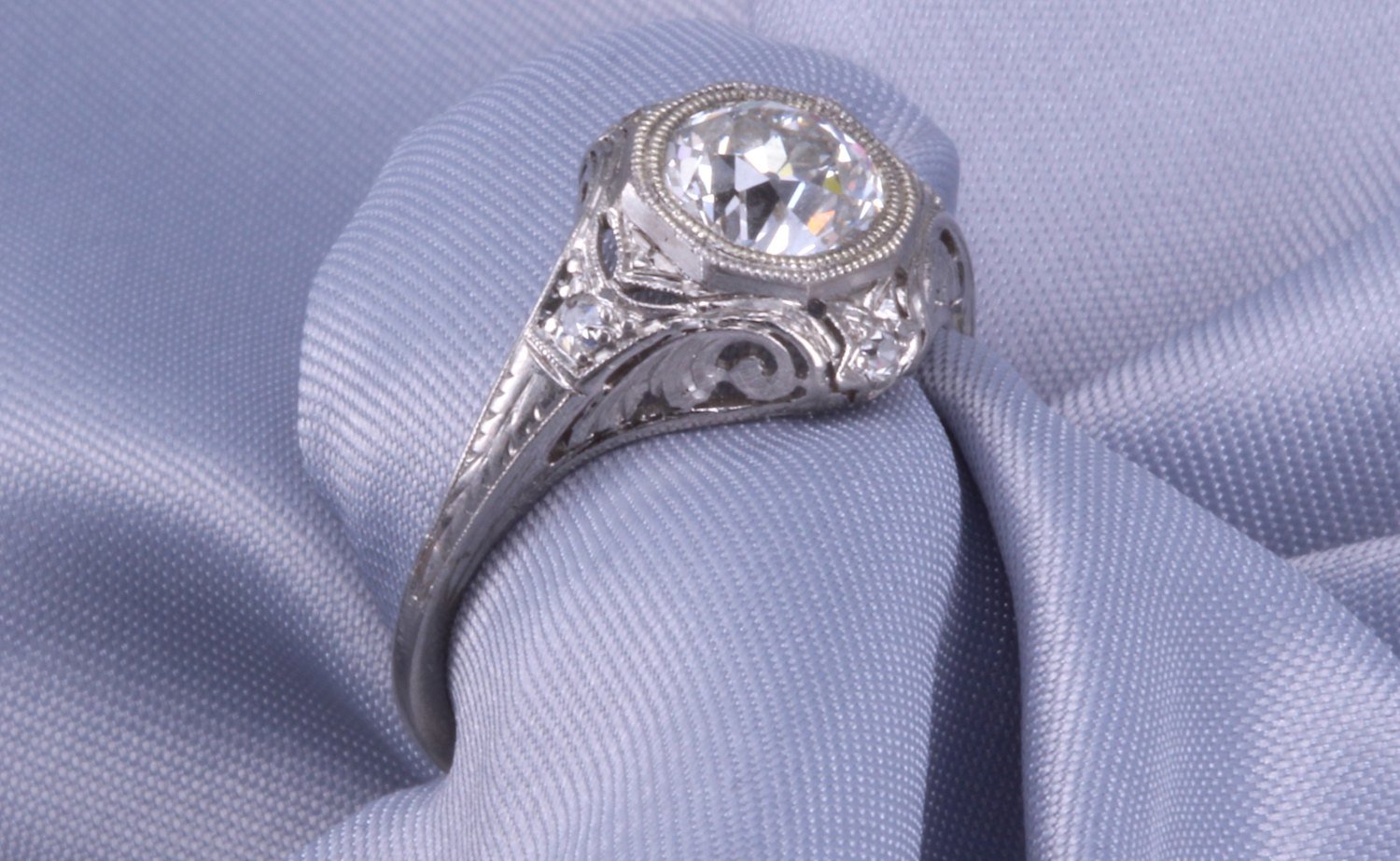
12 Aug Sell Antique Die-Cut Hand-Pierced Diamond Rings
We recently purchased a beautiful antique diamond ring, which was die-struck in platinum and then pierce-sawed by hand into a leafy scroll design. It is a truly gorgeous antique engagement ring (see image above). As San Diego jewelry buyers, it’s one type of diamond ring we always are interested in purchasing, paying a premium price to the seller.
Antique die-struck, hand-pierced diamond rings are known for their durability and exquisite detailing — showcasing a unique blend of artistry and technical precision. That is why some California brides, even today, will wear a family heirloom engagement ring that was created over 100 years ago in this manner.
If you are fortunate enough to own an antique diamond ring that was hand-pierced and sawed to perfection, keep reading to explore the history of this jewelry making tradition. If you would like to sell your ring, please contact us by leaving a voicemail at 858-251-3006 or sending a text message with photos of your ring to 619-723-8589.
Easy to Work With
Carl is a great jeweler and easy to work with. He handles a wide variety of services from buying jewelry to designing custom pieces for you. I sold some old jewelry to him, he had very fair prices transactions were handled in a timely manner
Careful Inspection
I recently sold a lot of fine jewelry that I had inherited from my mother. I chose Carl Blackburn because I wanted the pieces to find new homes, rather than be melted down or taken apart. Carl careful inspected and considered each piece before pricing it. He explained the quality of the gold in each piece, the techniques used to craft the pieces, and what went into his pricing. He appreciated the sentimental value of the items and actually had buyers in mind for several of them. I felt that he gave me a fair price the first time I came in, so I returned with additional items to sell a few weeks later. I’d highly recommend Carl Blackburn for selling and buying estate jewelry.
A Straight Shooter
I met with most of the Jewelers around La Jolla and no one was as knowledgeable or as helpful as Carl was to me. Carl Blackburn is a straight shooter and someone you can trust. C. Blackburn Jewelers will forever have my business and recommendation to all of my network for any future jewelry business.
Genuine & Friendly
Being at a downsizing stage of life, I decided to sell as much of my jewelry as possible, and luckily, I came across C. Blackburn Jewelers. I was scared of getting scammed and cheated. Carl had me sitting with him while he examined and evaluated my jewelry. He did not take it into a back room and tell me to return on another day.
He worked methodically and very professionally, answered all my questions, kept my expectations realistic, explained what he was doing as he worked. We also had a very pleasant conversation – he is down-to-earth, genuine, and friendly. I trusted him without hesitation. I was very pleasantly surprised by the outcome and felt I was very fairly treated. I was relieved that the process was stress-free, thanks to Carl’s very professional manner and his genuine friendliness. I recommend him highly, without reservation.
History of Die Struck, Hand-Pierced Antique Rings
The technique of die striking, followed by hand-piercing and sawing, became prominent during the Victorian and Edwardian eras (late 19th to early 20th centuries). These periods were characterized by a fascination with intricate jewelry that reflected the wearer’s status, taste, and sentimentality.
The Industrial Revolution, which introduced new machinery and techniques, played a significant role in popularizing die-struck rings. However, despite the industrial advancements, the demand for hand-finished details remained strong, leading to the combination of die striking with hand-piercing and sawing to achieve both precision and individuality.
Antique die struck rings were created using a technique where metal is stamped or pressed using a die (which is a mold made of hardened steel). This process allowed for the mass production of high-quality, durable rings with precise, sharp details.
The addition of hand-piercing and sawing, where jewelry artisans meticulously cut and shape the metal by hand, added a level of intricacy and uniqueness to each ring that machines alone could not achieve — which is why we see some antique diamond engagement rings crafted in this way.
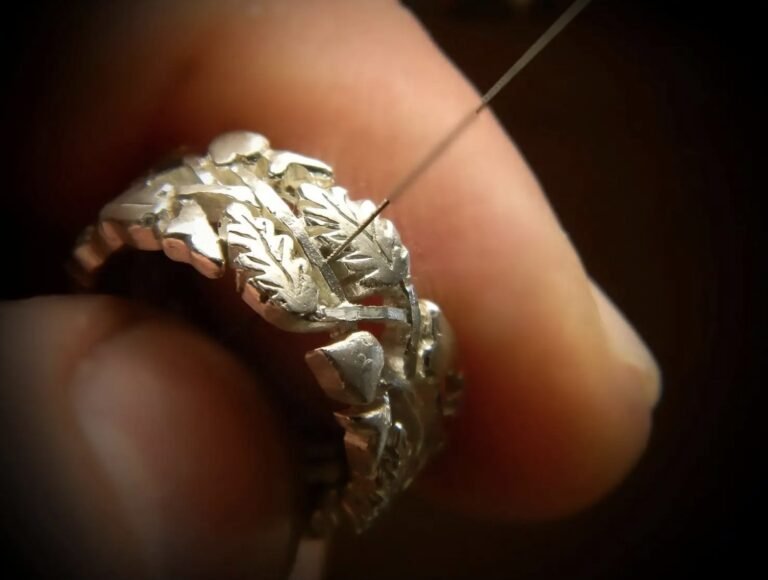
How Die Struck, Hand-Sawed Antique Rings Were Made
The creation of these antique rings began with the die-striking process. A sheet of metal, typically gold or platinum, was placed between a pair of dies, and tremendous pressure was applied to stamp the metal into the desired shape. This method ensured that the design was uniform and consistent, with crisp, well-defined details.
Once the ring was die-struck, the hand-piercing and sawing process began. This involved using a fine saw blade, often called a jeweler’s saw, to cut intricate patterns and motifs into the metal. This stage required immense skill and precision, as the artisan must carefully follow the design without breaking the delicate saw blades or damaging the ring.
Hand-piercing allowed for the creation of openwork designs, where parts of the metal were removed to create a lace-like effect. The result were a ring that, despite being produced through a mechanical process, bears the unmistakable mark of human craftsmanship.
After the piercing and sawing were completed, the ring was further refined through filing, polishing, and sometimes engraving. The final ring is a piece of fine jewelry that combines the durability and precision of die striking with the delicate, intricate beauty of hand-piercing and sawing.
The Metals Used in Antique Rings
The metals traditionally used in die-struck, hand-pierced rings are primarily gold and platinum. Gold, available in various purities such as 14k and 18k, was favored for its malleability, luster, and ability to hold fine details. Yellow gold was common in the Victorian era, while white gold and platinum became more popular during the Edwardian period.
Platinum, prized for its strength and resistance to tarnish, became especially popular in the early 20th century. Its durability made it ideal for the intricate work required in these antique rings, allowing for the creation of delicate, openwork designs that would withstand the test of time.
The cool, silvery sheen of platinum also complemented the delicate, ethereal motifs popular during the Edwardian era.
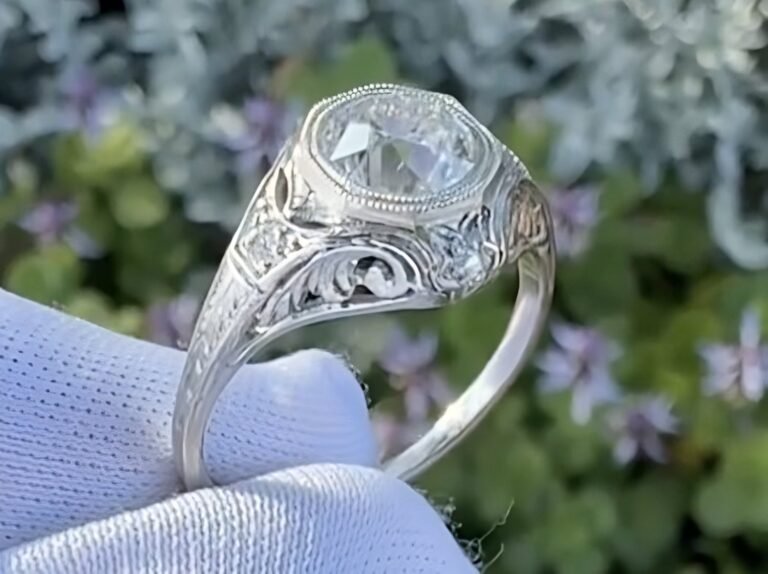
Popular Motifs and Their Significance
The motifs featured on antique rings that are die-struck and pierce-sawed reflect the cultural and artistic trends of their time. During the Victorian era, rings frequently featured romantic and nature-inspired motifs such as hearts, flowers, and leaves. These symbols were not only decorative but also conveyed deep personal sentiments, making the rings both beautiful and meaningful.
In the Edwardian era, antique ring motifs became more elaborate and often featured intricate lace-like patterns, garlands, bows, and scrolls. These designs were inspired by the light, airy fashions of the time and the era’s fascination with the elegance of the past, particularly the 18th century. The use of platinum allowed jewelers to create delicate, almost weightless designs that were both intricate and durable.
One of the reasons these motifs were so popular is that they resonated with the prevailing tastes and values of the times. The Victorian emphasis on sentimentality and the Edwardian appreciation for elegance and refinement are clearly reflected in the jewelry of these periods. The motifs were not only aesthetically pleasing but also carried personal and symbolic meanings, making these rings treasured keepsakes.
Recent Estate Jewelry Buys
Browse a collection of C. Blackburn Jewelers’ recent buys from sellers throughout Southern California.
Are Die-Struck, Hand-Pierced Engagement Rings Still Made?
Yes, there are some artisan jewelers who still make custom engagement rings using the die-struck and hand-piercing process. However, they are few in number, as this antique method of jewelry making is quite costly and time consuming.
During the mid 20th century die-casting was replaced by a method known as “lost wax casting”. This is a process where a wax model of the desired object is created, encased in a mold, and then melted away to leave a cavity that is filled with molten metal, forming the final piece once the metal cools and hardens.
Lost wax casting is the process that La Jolla jewelry designer Carl Blackburn (and most other fine jewelers) use when creating custom engagement rings and fine jewelry, because it has a number of benefits for couples who want to create a one-of-a-kind engagement ring.

The benefits that lost wax casting provide include:
Cost Efficiency:
Die-Striking: The die-striking process involves creating steel dies, which are expensive and time-consuming to produce. Each ring design requires its own set of dies, making it costly for fine jewelers to produce multiple or custom designs.
Lost Wax Casting: In contrast, lost wax casting is more cost-effective, especially for custom engagement rings and bridal jewelry. The process involves creating a wax model of the piece, which can be easily altered or customized before being cast in metal.
Flexibility and Design Complexity:
Die-Striking: While die-striking produces very durable and precisely detailed rings, it is limited by the design that can be stamped. The designs are typically more two-dimensional, unless the ring is hand-pierced and sawed (which requires much more time and money)
Lost Wax Casting: Lost wax casting allows for greater creativity and complexity in design. It enables the production of three-dimensional pieces with intricate, detailed forms that are not possible with die-striking. Custom jewelers can create more organic shapes, detailed textures, and complex patterns.
Customization and Prototyping:
Die-Striking: Customization is challenging with die-striking, as it requires new dies for each design variation, which is not practical for one-off or limited-edition pieces.
Lost Wax Casting: Lost wax casting is ideal for customization. Jewelers can easily modify wax models to create unique designs, making it a preferred method for custom jewelry. It also allows for easier prototyping, where a wax model can be adjusted multiple times before the final casting.
Contact C. Blackburn Jewelers Today
Whether you would like to sell an antique diamond engagement ring or have a custom-made engagement ring created, C. Blackburn Jewelers welcomes the opportunity to talk with you. Contact us today to have a friendly and informal chat with our owner Carl Blackburn, who is both a 2nd generation estate jeweler and a well-known jewelry designer for over 20 years.
Leave Carl a voicemail at 858-251-3006 or send him a text message at 619-723-8589. You can also send him an email via our contact form below.